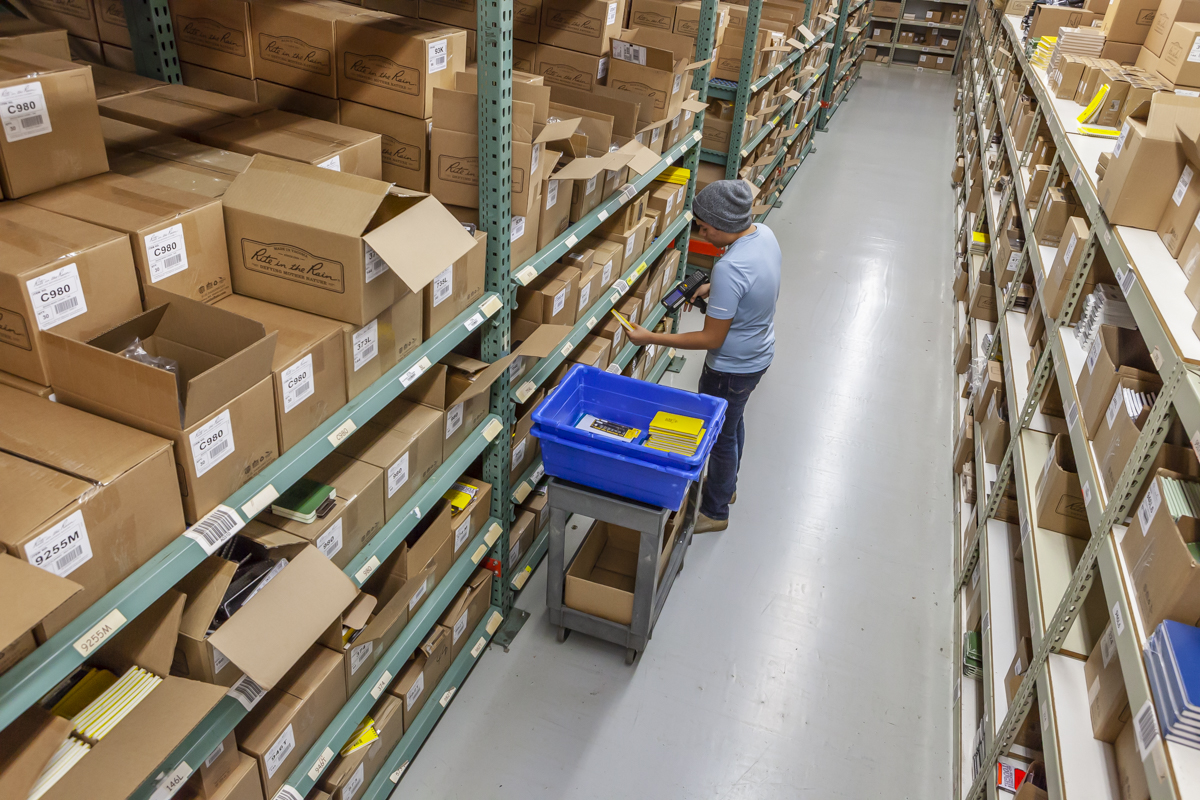
Manufacturers are always looking for ways to produce faster results and improve efficiency. When applied effectively to your day-to-day manufacturing procedures, lean warehouse management does just that. Lean Warehousing is being implemented in multiple different manufacturing companies, and yours could be one of them.
What is Lean Warehousing?
“Lean” is a common business tactic used to reduce unnecessary elements in a process or system in order to improve efficiency. Lean warehouse management is the specific application of this tactic to warehouse production. In other words, lean warehousing is identifying what efforts or expenses don’t yield benefits or add value to production. One example of waste is overproduction. If you produce more products than actual demand, you end up with an excess of products that may not be used. Producing only those that are needed will eliminate this waste and improve production (not to mention the reduction in costs). Lean warehouse management identifies common areas of waste and outlines a series of steps to eliminate them and improve efficiency.
Lean warehousing can be a significant asset to your manufacturing company if effectively implemented. There are essentially five steps (5s) of lean warehouse management that can eliminate waste in your company:
1. Sort
The first step is to sort through your warehouse. Look at your inventory and determine what is necessary and what is not. There are ways to cut back on expenses and unnecessary supplies, equipment, or products. This could look like a variety of different things. Considering some of these questions can help you determine what areas you could improve:
- Does your warehouse have a functional workflow? Are there ways to create a more efficient path or workstation? Can you eliminate some physical obstacles that get in the way of employees (for example, moving boxes of inventory to another place if they’re in the way of employees’ work path)?
- Are there technological advances you could make to reduce physical products in the warehouse? Can you cut down on paper products and instead use scanners, printers, etc.?
2. Straighten
The next step is to straighten out the organization of your warehouse. This could look like finding the best place for tools or necessary products, and ensuring the tools your employees use most often are accessible. You could also organize your warehouse better by placing signs around that remind your employees of where things are, the proper procedures, and the general workflow of the warehouse.
More specifically, these could be signs that outline what employees are expected to do at the end of their shift (charging or cleaning equipment, putting away tools or supplies, preparing anything for the next shift, etc.). It’s important to evaluate what your warehouse needs specifically in order to arrange your supplies and workflow successfully.
3. Shine
This step focuses on post-shift clean-up. There’s no doubt that “a cluttered space means a cluttered mind.” When it comes to manufacturing warehouses, a messy space means messy production. Keeping a clean warehouse is essential to make sure it operates at its highest function.
Regular safety inspections are required for a warehouse to continue to operate. Requiring end-of-shift or nightly cleaning from employees helps your workplace to stay well maintained and decreases the possibility of committing safety violations during an inspection. Improving the maintenance and cleanliness of your warehouse may require you to develop new standards and procedures. It’s important to be open to the steps it may take to improve the overall function of your warehouse.
4. Standardize
It can be beneficial to implement signs that outline procedures but ensuring your employees carry out that action is imperative. Whether you are changing important processes or simply adding post-shift cleaning tasks, it’s necessary to ensure your employees are well aware of and equipped to follow the new standards. Providing new training (videos, personal walkthroughs, etc.), holding staff meetings, or simply planning brief announcements before each shift, are all ways to ensure your employees understand the new procedures they’ll be required to follow.
If you’re implementing many different changes, consider retraining employees to make sure they understand the new procedures. Otherwise, brief announcements can work just fine. No matter how you decide to inform your workers of new changes, it’s essential to make sure all employees are on the same page.
5. Sustain
After applying the above steps, keeping standards and processes upheld is the only way you will see improvements in efficiency, quality, and production. If you fail to hold employees to the new standards, you will find yourself in the same spot you were before implementing lean warehouse management. Plan regular check-ins with workers to make sure procedures are being followed and the organization is being kept. Likewise, do regular walk-throughs to check the cleanliness and upkeep of your warehouse. This will reveal whether processes are being followed, what areas to focus on, and any challenges with the new standards. It’s also important to ensure that all current employees understand new procedures and that new employees are trained and well equipped to carry out the warehouse systems.
If for any reason standards aren’t improving production and overall warehouse function, consider creating new procedures that better fit your manufacturing needs. Communicate with workers about any issues with new standards and seek to solve those with necessary measures. Applying lean warehouse management is about the continuous assessment of resources and methods. Regularly assessing manufacturing systems is the only way to sustain improvement. All levels of workers have a responsibility in carrying out new and improved standards. It is the management’s job to instill discipline, order, and diligence in the workplace.
Lean warehousing is all about eliminating waste and finding what works for your manufacturing company.
It’s important to evaluate these five different areas of your warehouse and be open to change. Continuous improvement of working conditions coincides with continuous improvement in production. Working conditions are important to employees as well. By amping up standards and systems, and by regularly assessing successful or unsuccessful standards, you can both attract and retain employees.
Lean warehouse management requires the assessment and implementation of new standards, which ultimately leads to increased efficiency, faster production, better working conditions, and sustained improvement. Knowing where to start can be challenging, which is why it can be beneficial to bring in outside resources. Impact Washington, Washington state’s local MEP, is here to help you apply lean warehousing in the most effective way. Contact Impact Washington today and set your warehouse up for success!